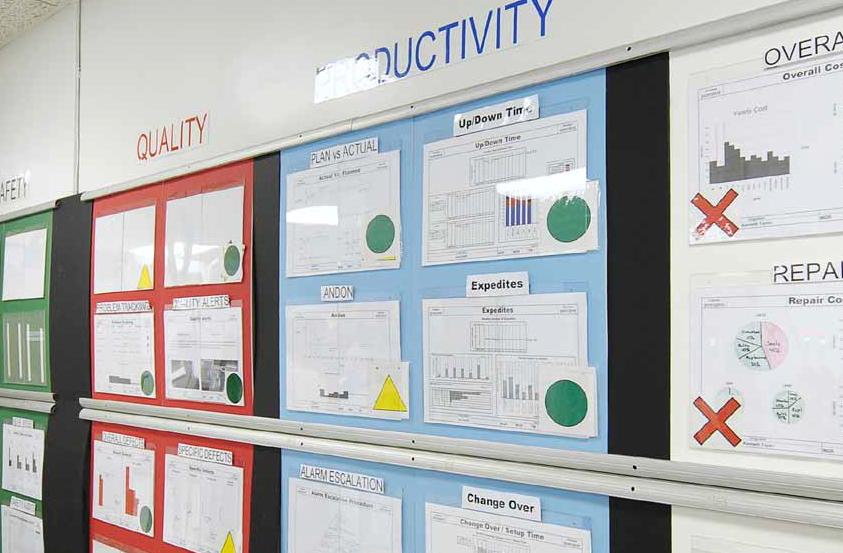
The University of Kentucky’s Lean Systems Program is perhaps the closest you can come to understanding lean as Toyota sees it. Program director Ken Kreafle and Kathleeen Jeurisson of Lake Region Medical, talk about the people side of true lean.
It’s hard now to imagine a world without lean. But at the time Toyota’s Taiichi Ohno began developing this revolutionary new approach to manufacturing just after the Second World War, his thinking was completely ground breaking. There were no lean tools or processes to fall back on. He was working from scratch. Today, lean has spread around the world, delivering vast improvements to the manufacturing sector, and is spreading quickly to all areas of business and industry, from health delivery and retail through to financial services and government.
Yet curiously, the first attempts to transfer the philosophy beyond the walls of Toyota were far from successful, in spite of the Japanese company’s commitment to sharing its knowledge. The magic touch simply did not transfer. Then, during the 1990s, Toyota worked with the University of Kentucky’s (UKy) College of Engineering to develop the Lean Systems Program (LSP) to help impart the true philosophy to non-Toyota companies in the US.
The program’s director, Ken Kreafle, is a Toyota executive, and provides a continuous link with the latest lean thinking from the company that initiated this revolutionary approach. Located just 17 miles down the road from Toyota’s Georgetown plant, the first wholly owned subsidiary in the US, the University’s engineering college was an obvious and logical choice for a Toyota teaching program.
“We don’t see ourselves as consultants,” Kreafle said. “We don’t go in and impose change to recreate an exact copy of the Toyota Production System (TPS). Our aim is to transfer true lean skills and knowledge to a company’s leadership so they are able to develop their own lean system, custom-tailored to their company and their industry.”
The approach developed by UKy is very much top down, and begins with a Lean Executive Leadership Institute - a one to three day course for the company’s top executives. Kreafle believes the importance of this cannot be over emphasized. “What we will be aiming to do is adjust the entire company’s culture and operational system, and only the executive team has the authority to do that,” he explained. “Therefore, right from this initial stage we strive to enlighten them that their involvement is absolutely essential, and they cannot delegate the responsibility to a lower level in the company.”
Having gained this level of commitment at the executive level, the second step is the Lean Certification course, and this is the real meat of the program. Targeted at middle management - those who will train the workforce and drive the implementation forward - it’s a discovery-based learning program held at the university for one week a month over a three month period. The aim is to impart an in-depth understanding of lean along with elements of change management, and to develop leadership skills in lean implementation. “In this context leadership means a vision of what they want to achieve and a clear ability to motivate others to accomplish that vision,” Kreafle said.
Chaska, Minnesota-based Lake Region Medical, an international manufacturer of minimally invasive guide wire delivery systems for cardiovascular diagnostic and interventional devices, has been working with the university through the lean systems program. “After the two day executive course, we had complete buy-in from above and that was crucial,” said continuous improvement director, Kathleen Jeurissen. “We then created a continuous improvement department with myself and three lean coordinators. And we went to Kentucky for the three week training course.”
On returning to Chaska, the real work began. Imparting knowledge about lean and bringing the workforce onboard was a critical ingredient in making it work. “As trainers, we took employees from each department through an introduction course on continuous improvement, so they learned about the seven wastes, 5S, problem solving, flow and all the other principles of lean,” Jeurissen said.
“Then we took them through a simulation factory, and this was one of the valuable insights we took away from our training in Kentucky: how important it was for employees to understand what you’re trying to do and why, before you begin implementing it. If they don’t, they will eventually revert to old practices. Once we’d done that, we had enthusiastic people engaged in leaning out their own area of the plant. Then it became more of a partnership.” Alongside training and engaging the workforce, the continuous improvement team tackled 5S, to get the shopfloor in order.
From this stage onwards in any implementation, the University offers specialized field teams of experienced former Toyota members to go into the plant to provide support and coaching in specific areas of need. Additional courses are also available on specialized topics such as the people side of lean, problem solving, and standardized work.
From Lake Medical’s perspective, the company was experiencing difficulty coming to grips with eight-step problem solving. “The practitioners from the university came to our facility and during the first week they led the eight-step problem solving activities, teaching as they went,” she explained. “They then left us working with the problem, and we had weekly conference calls with them. The second time they were here, we worked on a new problem and we led the activities, while the practitioners helped us understand how we could improve what we were doing. After that, they mentored us. It took some time for it to finally click, but now we’ve got it, and we’re now training and implementing it.”
The content and teaching style of the LSP courses are key to their success, and they are based on two key reference points: understanding the thinking processes through which Taiichi Ohno developed the TPS, and Toyota’s thinking today.
“Our research has shown us that there are three types of lean implementation,” Kreafle said. “Type I is how Toyota does it internally, and that’s the way I learned it at Georgetown. We had several hundred Japanese coming to work with us there, so we were marinated in it like a piece of meat. They would let us do it first and then correct us and work with us and talk to us.” Type II implementation, meanwhile, is how Toyota implements TPS into its supplier base, and Type III is the LSP which aims to circumvent many of the common pitfalls in lean implementation.
“Many of the difficulties companies experience with implementing lean is that they look at a typical Type I Toyota implementation and don’t see the embedded culture. Therefore they believe it is all about the tools,” Kreafle continued. “It isn’t. The whole process is a cultural adjustment, and it’s all about people. It’s about motivating and engaging with every member of staff so they play a part in improving the work they do and removing waste. And this process involves a strong discipline of systematic problem-solving based on facts and data, and then moving on to recurrence prevention through standardization.”
Of course, lean improvement never has an end. While many see this as a negative thing, it’s not. Companies that are continuously adapting are not only more efficient, but they are more competitive and nimble, and far more able to respond to changes in technology, the economy and the marketplace - all of which are crucial for competitiveness in today’s uncertain world.
DOWNLOAD
Uni.Kent-NA-Jan12-Bro-s.pdf